The Importance of Tubes and Fittings in Modern Industry
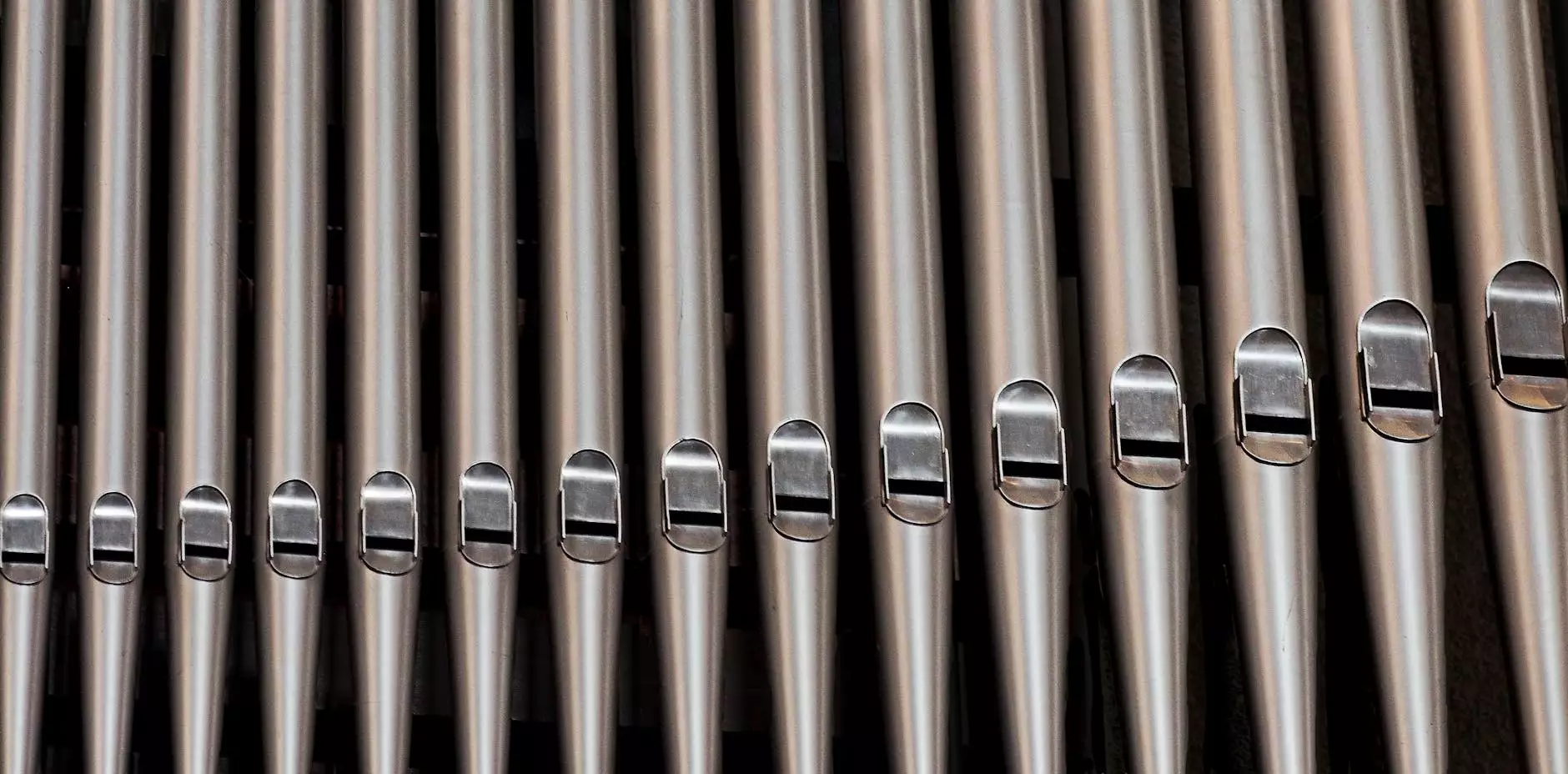
Tubes and fittings play a crucial role in various industrial applications, contributing significantly to the efficiency and effectiveness of fluid transfer systems. From the oil and gas sector to pharmaceuticals and food processing, these components ensure the safe and reliable transportation of liquids and gases. This article delves deeply into the various types of tubes and fittings available, their applications, and the ever-evolving technology that surrounds them.
Understanding Tubes and Fittings
At the core of any fluid transport system are tubes and fittings. They form the backbone of pipelines used in numerous industries, providing a reliable means of conveying substances from one point to another. Understanding the various types of tubes and fittings is essential for making informed decisions on the materials best suited for specific applications.
Types of Tubes
Tubes are usually characterized by their diameter and wall thickness. Here are some common types:
- Stainless Steel Tubes: Known for their corrosion resistance and strength, stainless steel tubes are widely used in food processing and pharmaceutical industries.
- Copper Tubes: Often used for plumbing and HVAC applications due to their excellent thermal conductivity.
- Plastic Tubes: Lightweight and resistant to corrosion, plastic tubes are popular for chemical applications.
- Aluminum Tubes: Offering a good strength-to-weight ratio, aluminum tubes are often used in structural applications.
Types of Fittings
Fittings are essential components that connect sections of tubes and pipes. Each type is designed for specific applications:
- Tube Fittings: These fittings are used to connect tubes in various configurations. They can be found in both single and double ferrule designs.
- Ferrule Fittings: These fittings consist of a ferrule that creates a tight seal around the tube, ensuring no leaks occur.
- Forged Pipe Fittings: Made from high-strength materials, these fittings are designed for high-pressure applications.
- Threaded Pipe Fittings: Available in various materials, these fittings feature threads that allow easy connection of pipes.
- Flanges: Used for bolting pipes together, flanges create a strong, leak-proof connection in high-pressure environments.
The Role of Tubes and Fittings in Different Industries
The versatility of tubes and fittings makes them suitable for a broad range of industries, each with unique requirements:
Oil and Gas Industry
In the oil and gas sector, tubes and fittings are crucial for both upstream and downstream operations. High-pressure applications demand fittings that can withstand severe conditions:
- Forged Pipe Fittings: Essential for connecting pipes transporting oil and gas under high pressure.
- Check Valves: Prevent backflow and protect the integrity of pipelines.
Pharmaceutical Industry
In pharmaceuticals, the integrity of fluid transfer systems is paramount:
- Stainless Steel Tubes: Hygienic and easy to sterilize, they are ideal for transporting liquids.
- Single Ferrule Tube Fittings: Provide reliable connections that maintain system cleanliness.
Food Processing Industry
The food industry operates under strict regulations, making material selection critical:
- Plastic Tubes: Offer flexibility and corrosion resistance for sugar and beverage production.
- Ball Valves: Commonly used to control flow in food processing lines.
Choosing the Right Tubes and Fittings
Selecting the right tubes and fittings involves considering various factors, including:
Material Compatibility
Materials must be compatible with the liquids or gases they will be transporting. For instance, stainless steel is often chosen for its corrosion resistance in hostile environments.
Pressure and Temperature Ratings
Components should meet the specific pressure and temperature requirements of the application. This ensures the longevity and reliability of the system.
Connection Type
Different applications may require different connection types, such as threaded, welded, or flanged connections. Each method has its advantages and disadvantages.
Innovations in Tubes and Fittings Technology
The industry is witnessing significant advancements in tube and fitting technology. Some innovations include:
- Smart Fittings: These include sensors that provide real-time data on pressure and flow rates, helping prevent failures.
- Advanced Coatings: New coating technologies enhance the corrosion resistance of pipes and fittings, prolonging their lifespan.
- 3D Printing: This technology allows for the rapid prototyping of custom fittings, facilitating quick adaptations in industrial setups.
Conclusion
In conclusion, the significance of tubes and fittings cannot be overstated. They are vital components across a multitude of industries, ensuring the safe and efficient transfer of fluids. Understanding the various types, applications, and innovations in this field can empower businesses to make informed choices that enhance their operational efficiency and safety.
As industries continue to evolve, so too will the demand for high-quality, reliable tubes and fittings. Companies like Tech Tubes (techtubes.in) lead the way in providing comprehensive solutions that meet the needs of modern industrial applications.