Understanding Prototype Injection Molds: An In-Depth Guide
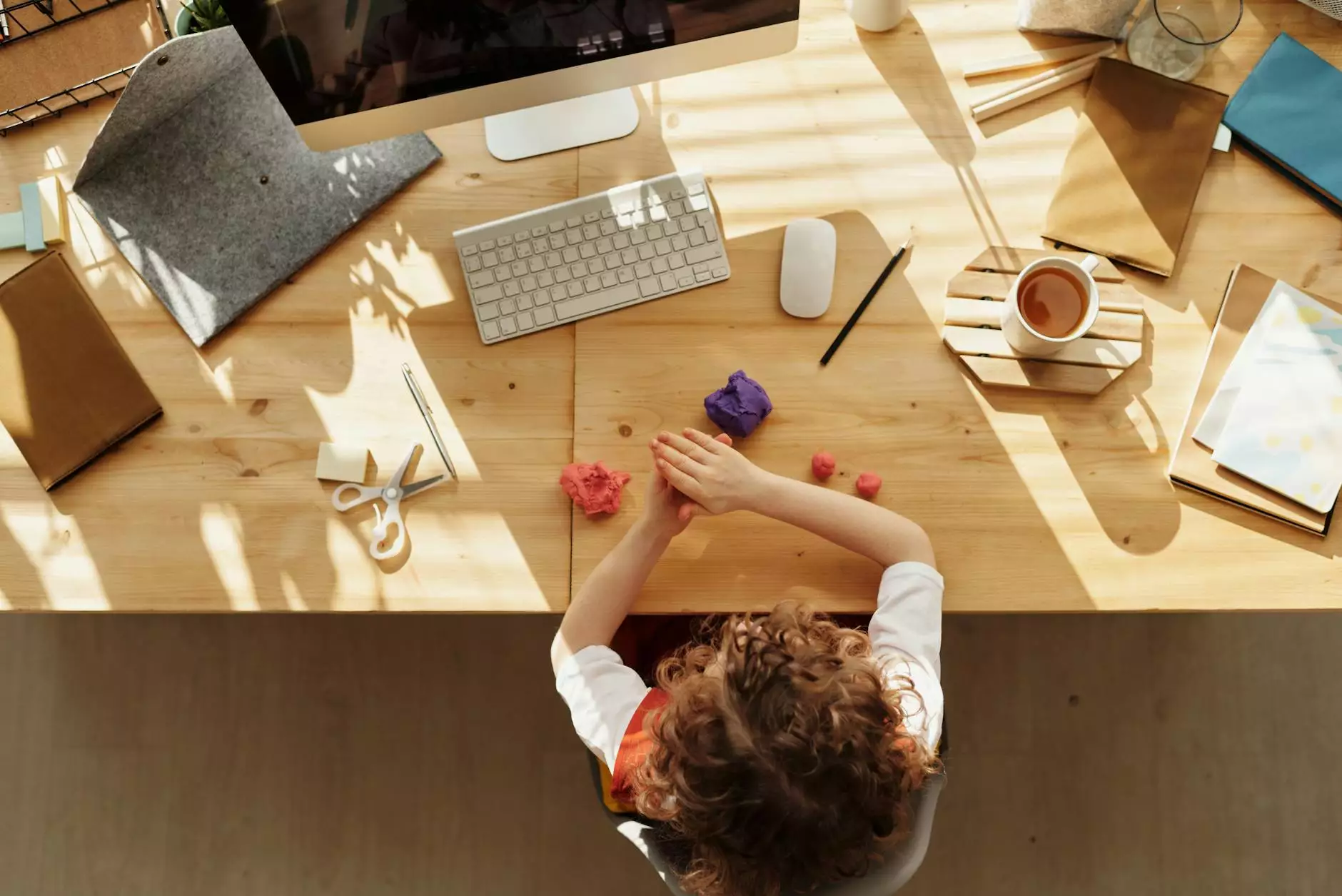
In the rapidly evolving world of manufacturing, prototype injection molds play a critical role in creating precise, high-quality parts and components for various applications. This comprehensive guide delves into what prototype injection molds are, their benefits, applications, and how they contribute to the metal fabrication industry. With insights from DeepMould.net, we aim to equip you with the knowledge needed to make informed decisions regarding injection molding processes.
What Are Prototype Injection Molds?
Prototype injection molds are crucial tools designed for creating parts from thermoplastic materials. These molds enable manufacturers to produce highly accurate prototypes quickly and efficiently. The process involves injecting molten material into a mold cavity, forming a specific shape that can be replicated numerous times. This technique not only streamlines production but also offers numerous advantages when developing new products.
Benefits of Using Prototype Injection Molds
Utilizing prototype injection molds comes with several significant benefits:
- Speed: The rapid production of prototypes allows companies to accelerate their time to market.
- Cost-Effectiveness: Although the initial investment in molds can be high, the per-unit cost decreases significantly with higher volume runs.
- Material Variety: A wide range of materials can be used, allowing for flexibility in product design and functionality.
- Precision: These molds provide consistency and tolerance in manufacturing that is difficult to achieve with manual processes.
- Testing and Iteration: Prototypes can be tested and iterated quickly, facilitating design improvements before moving into mass production.
Applications of Prototype Injection Molds
The applications of prototype injection molds span across numerous industries, including:
- Automotive: Used for producing interior and exterior components, helping manufacturers develop parts that meet stringent safety and quality standards.
- Consumer Electronics: Essential in creating housings, buttons, and other critical components for devices.
- Medical Devices: Vital for producing parts that require high precision and biocompatibility.
- Packaging: Molds are utilized in creating packaging solutions that are both functional and aesthetically pleasing.
- Toys: Prototype molds help in designing safe, engaging toys while optimizing production costs.
How Prototype Injection Molds Work
The process begins with the design of the product. Engineers and designers work closely to create a CAD (Computer-Aided Design) model of the required component. This model serves as the foundation for the injection mold design.
Steps in Creating Prototype Injection Molds
- Design Phase: Create a detailed 3D CAD model of the part to be manufactured.
- Mold Design: Develop a mold that will accommodate the part's specifications, including any necessary cooling channels.
- Material Selection: Choose the appropriate thermoplastic material based on the desired properties of the final product.
- Mold Fabrication: Fabricate the mold using CNC machining or other advanced manufacturing techniques.
- Injection Phase: Inject molten plastic into the mold and allow it to cool and solidify.
- Post-Processing: Remove the part from the mold and perform any necessary finishing work.
Choosing the Right Manufacturer: Why DeepMould.net Stands Out
When it comes to selecting a partner for your prototype injection molds, the choice of manufacturer can significantly influence the outcome of your project. DeepMould.net distinguishes itself through:
Expertise and Experience
With years of extensive experience in the industry, DeepMould.net is equipped with the knowledge and tools necessary to produce high-quality molds efficiently. Our engineers and technicians are skilled in the latest fabrication techniques, ensuring that every mold is crafted to meet the highest standards.
Advanced Technology
We leverage state-of-the-art technology in our mold production processes, employing CNC machining, 3D printing, and advanced simulation software to enhance accuracy and efficiency.
Customized Solutions
Understanding that every project is unique, we offer tailored solutions that fit specific client needs, from design alterations to material selection, ensuring the final product meets precise requirements.
The Future of Prototype Injection Molds
The landscape of manufacturing continues to evolve, and with it, the processes surrounding prototype injection molds. Innovations in technology, such as the integration of automation and smart manufacturing, pave the way for even more efficient production methods. Trends such as additive manufacturing are also beginning to complement traditional injection molding, offering new ways to create complex geometries that were previously unachievable.
Conclusion
In summary, prototype injection molds are a vital component of modern manufacturing, enabling rapid prototyping and ensuring that products are designed and manufactured with precision. By choosing DeepMould.net, you gain access to unparalleled expertise, advanced technology, and customized solutions that drive your projects to success. Invest in quality and innovation; your next breakthrough product begins with understanding the power of injection molding.
Get Started Today!
If you are ready to take the next step in your manufacturing journey, contact DeepMould.net today to learn more about our prototype injection molds and how we can help bring your ideas to life!